Efficient solution for clinker brick facades: With HEBAU exposed aggregate concrete paper, precast concrete facades with clinker brick slips can be produced much more easily and cleanly.
The March issue of "BFT INTERNATIONAL" reports of practical tips to facilitate the production of thin-brick-embedded precast façade elements, using HEBAU retarder paper. Click here for the original BFT article, from which we have quoted (March issue, vol. 89; S.16-18).
"One of the architectural trends in building construction in recent years has been and continues to be façades with brick surfaces. While in certain regions brick wall and façade surfaces are an everyday traditional construction method, it is discernible that thin clay brick embedded precast concrete façade elements are gaining importance also nationwide, wether designed as panels or as sandwich element.
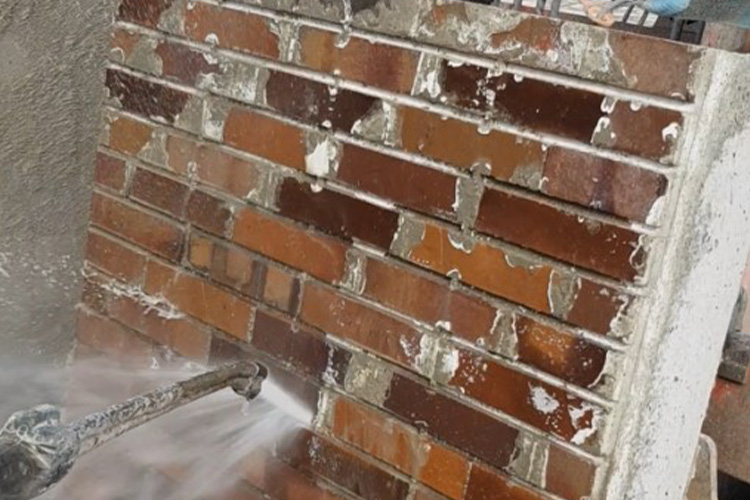

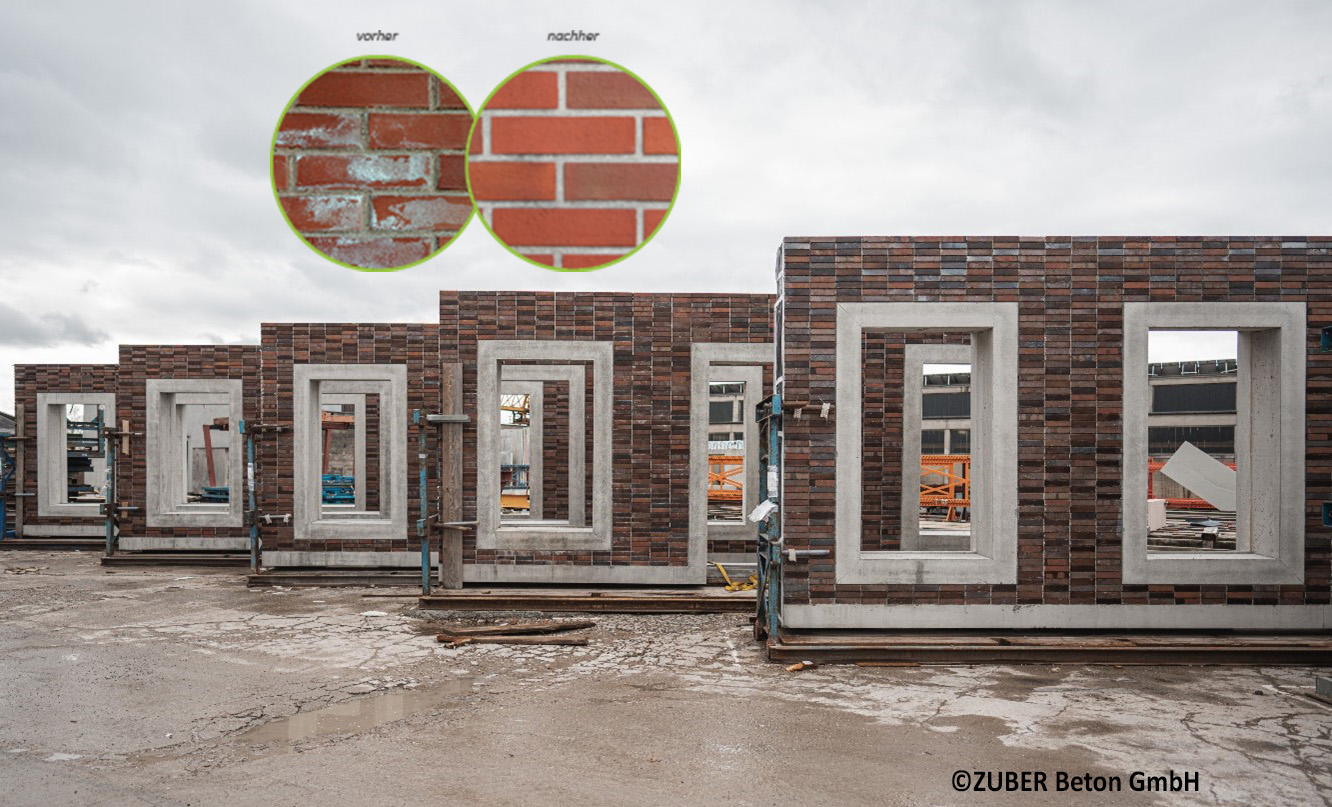
Retarder Paper as a mould inlay and contact zone
However, when designed as a precast concrete surface there are some challenges in terms of craftsmanship when placing or fixing the thin brick in the correct position on the mould surface before the mould is filled with concrete. Various aids are available for this purpose (wooden strips, joint tapes, formliners etc.), but it must be taken into account that the bricks have size tolerances due to the manufacturing process. Also, it is almost impossible to prevent cement paste from seeping through along the sides and towards the surface of the brick to harden there. Since the surfaces of the brick are often rough and to a certain extent absorbent, this contamination can usually only be removed with considerable cleaning effort.
HEBAU offers an easy solution - HEBAU Retarder Paper (WB-Paper)
To simplify this cleaning procedure, experienced precast concrete plants use paper coated with a surface retarder (also known as exposed aggregate concrete retarder paper) as an intermediate layer and contact zone in between the mould and the brick surface. Therefore, the cement paste that reaches the surface of the brick cannot harden there and is simply removed with a water jet after demoulding the precast element.
Download: Step by Step Guide
Long term observations pay off
When using formliners made of polyurethane or similar, in which the design pattern and the positioning of each brick are represented by the corresponding formliner texure, it is possible to work with cut-to-size retarder paper strips. If there are considerable size tolerances of the brick, a thin stretchable cloth can be treated with a liquid surface deactivator befor using this as the intermediate layer between the formliner and the brick surface. If no such stretchable cloth is available, a surface deactivator (to be determined in a preliminary test) can also be applied directly to the formliner or brick surface.
Marcus Herrfeld, managing director at HEBAU explains that, "Our observation over many years have shown that only certain surface deactivators (also called exposed aggregate surface retarders) are suitable for the mould surface materials, do not affect adjacent mould parts, and leave a near sterile brick surface that is also suitable for subsequent surface protection products such as anti-grffitit coatings. Therefore, expert consultation is recommended."
Text: "BFT INTERNATIONAL" Magazine March, vol. 89; p.16-18
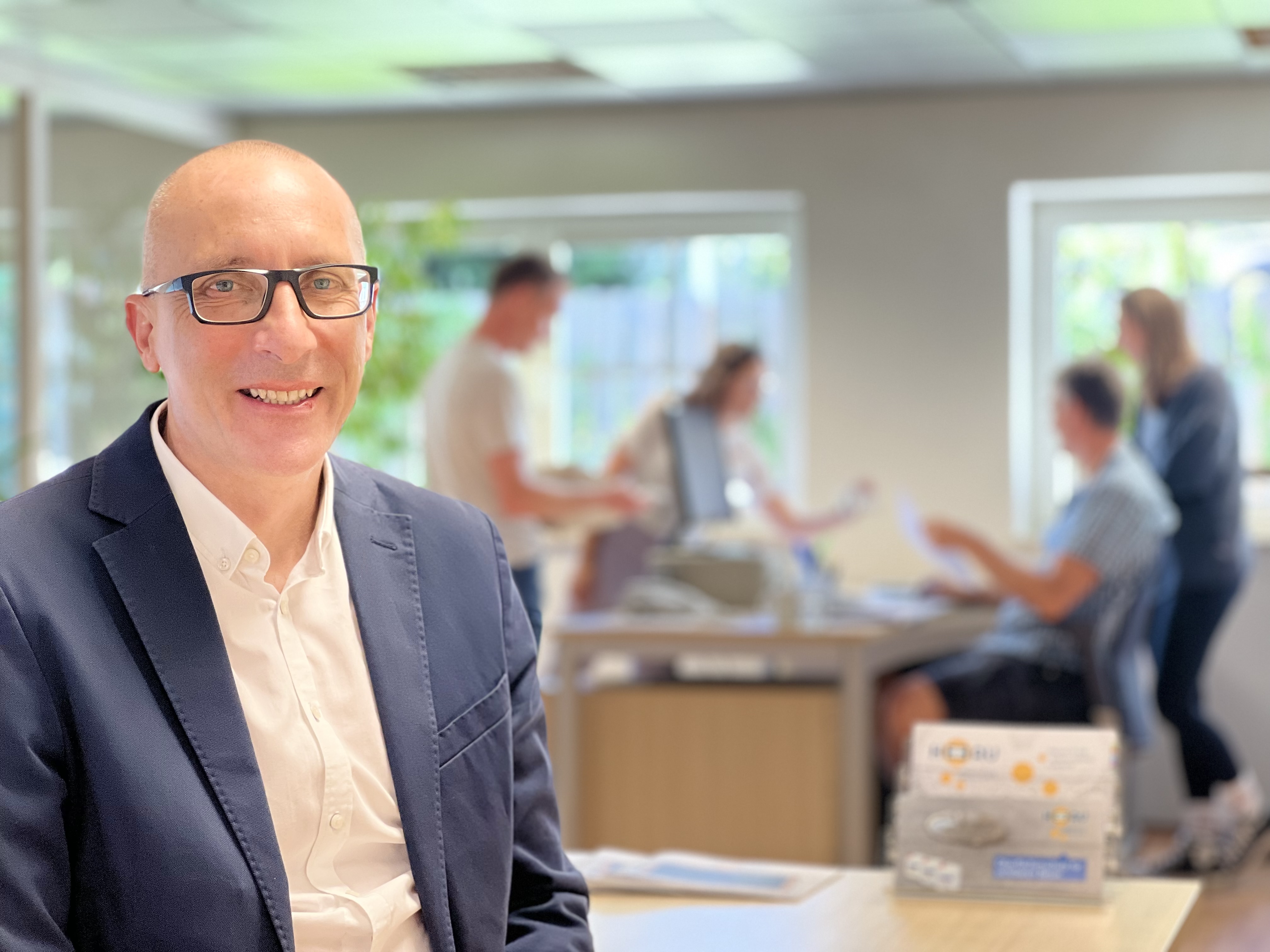